A CASE STUDY: THE TRANSFER SYSTEM FOR CROWN LIDS
- 15 September 2021
- Posted by: wp_nick
- Category: News
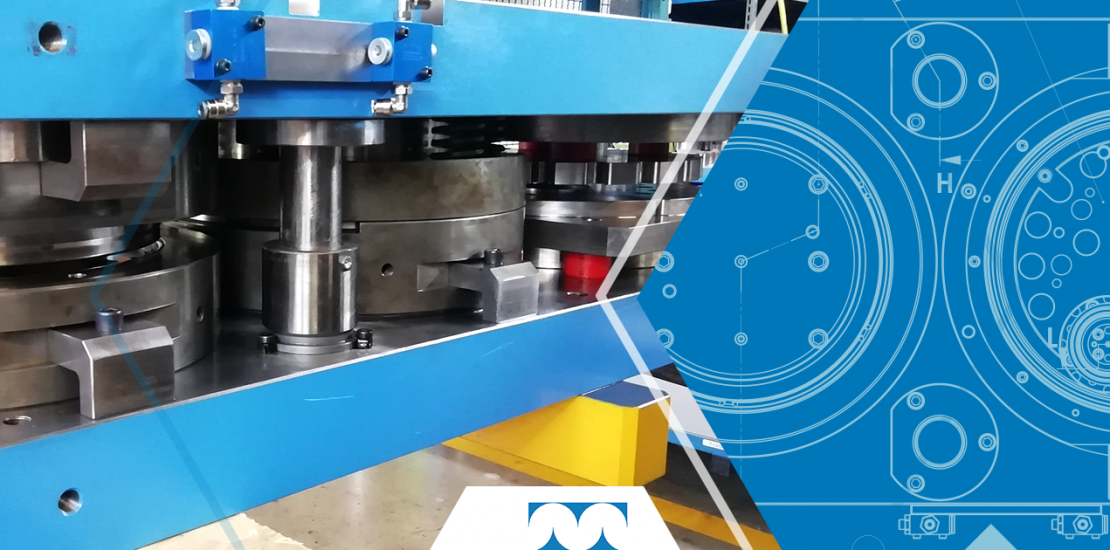
We managed to combine quality and product optimisation with considerable savings for our customers: let’s find out together how we did it.
OUR CROWN LIDS
Industrial containers, also called general line containers in our field, have no secrets for us at ETT. This is why our expertise is trusted by our customers throughout Europe.
We have already manufactured dies for different sized crown lids, which are generally used to close paint cans. In particular, we have set up presses which made already drawn crown lids with an outer curl in a single operation, for both Ø236 and Ø286 can sizes.
CRITICAL ISSUES AND THE ART OF COMPROMISE
This solution consisting of a single operation, i.e., a single die which cuts, draws, and curls, comes at the price of the quality of the final product. Therefore, it is necessary to find a compromise in optimising these three operations to reduce wrinkles and scratches in the paint. It’s a delicate balance, but it allows the customer to save a lot on machinery and equipment, by using a single press instead of three and thus reducing dies and transportation thereof.
A transfer system fitted on appropriately sized presses can manage in a single machine a three-station die, which differentiates these three operations to optimise the quality of the product with a reasonable investment.
Basically, we at ETT have developed an integrated system which makes the crown lid in three distinct stages, without any need for wide spaces and a lot of machinery, which would require maintenance and operators. We aim at engaging with those producers for which, just like us, the quality of their products always comes first and who want to offer competitive prices at the same time.
HOW IT WORKS
For the press type required by this system, the feeding must be a single, possibly scrolled, strip feeding to optimise the tin plate consumption.
For this project we completed a few months ago, we started from a sample of the finished crown lid our customer wanted to obtain.
The die passes through a first cutting station, where from the tinplate strip we obtain what we in the business call a flat blank (“pizza” in Italian), i.e., a simple shaped cutting, without ribs and draws.
The second station receives the component from the first station and forms the crown lid, by drawing it and making the anti-locking notches, which are typical of the general line products.
The third station receives the drawn crown lid and curls outwards its external petals. This is how we get the finished product.
The sizes and the weight of the die (that can reach up to 1,400 kg with the spacers for the press under consideration) made it necessary to carry out several tests to develop the three-staged system. To avoid having to move multiple times the complete equipment from our customer’s production facility to ours in Parma, we manufactured some adapter plates to fit one station at a time on our test press in our workshop.
These plates were manufactured to manage all three operations: they are not part of the final system, but they only speed the tests up.
At the end of the first die manufacturing step, we performed internal testing to try out the cutting station.
The sampling obtained from the tests of the first station was used for the tests of the second drawing station.
To avoid the usual forming of wrinkles on the external surface of the crown lid, we paid special attention to the drawing die diameter: in other words, we reduced the clearance available to the tin plate for the formation of these wrinkles.
We avoided scratches in the inside of the crown lid with an adequate punch radius.
We used the samples obtained for the tests of the third curling station, where a careful polishing of the curler allows both not to damage the paint and to optimise the management of special matted-painted lithographies, which are very sensitive to scratches.
immagine
The valuable support and the extensive expertise ensured by our customer were crucial in carrying out the tests. Moreover, an excellent team work has led to an outstanding result. And once again our technicians had the opportunity to share their knowledge, exchange views and grow professionally.
For this is exactly what we do, every day: never stop learning and getting better. Together, always.