UN CASO DI STUDIO: IL SISTEMA TRANSFER PER COPERCHI ALETTATI
- 15 Settembre 2021
- Posted by: wp_nick
- Categoria: News
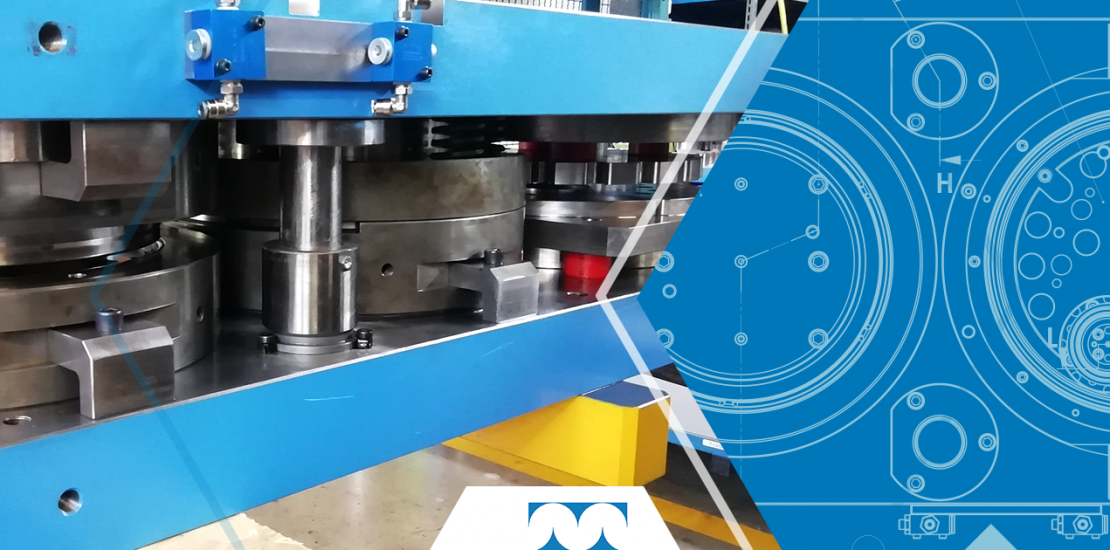
Scopriamo insieme come siamo riusciti a combinare la qualità e l’ottimizzazione del prodotto con un risparmio notevole per il cliente.
I NOSTRI COPERCHI
Per noi di ETT i contenitori industriali, definiti nel nostro settore contenitori general line, non hanno segreti. La nostra esperienza è infatti riconosciuta a livello europeo da tutti i nostri clienti.
Abbiamo già realizzato stampi per coperchi alettati di varie dimensioni, generalmente utilizzati per chiudere bidoni di vernice. In particolare, abbiamo attrezzato presse che realizzavano coperchi già imbutiti e con ricciolo esterno in una singola operazione, per formati di bidone sia Ø236 sia Ø286.
LE CRITICITÀ E L’ARTE DEL COMPROMESSO
Questa soluzione di un’unica operazione, quindi un unico stampo che taglia, imbutisce e ricciola, va a scapito della qualità del prodotto finale. È quindi necessario trovare un compromesso nell’ottimizzare le tre operazioni per contenere grinze e graffi sulla vernice. Un equilibrio delicato, che permette però al cliente di risparmiare molto in macchinari e attrezzatura, utilizzando un’unica pressa invece di tre e riducendo i relativi stampi e trasporti.
Un sistema transfer montato su presse di dimensioni adeguate può gestire in un unico macchinario uno stampo a tre stazioni, che differenzi le tre operazioni in modo da ottimizzare la qualità del prodotto con un investimento congruo.
In pratica, noi di ETT abbiamo sviluppato un sistema integrato che costruisce il coperchio in tre momenti distinti senza bisogno di ampi spazi e molti macchinari, che richiederebbero manutenzione e operatori. Il nostro obiettivo è interagire con quei produttori che, proprio come noi, mettono sempre la qualità dei loro prodotti al primo posto e che vogliono comunque offrire prezzi concorrenziali.
COME FUNZIONA
Per la tipologia di pressa richiesta da questo sistema, l’alimentazione deve essere da striscia, ovviamente singola, eventualmente scrollata per ottimizzare il consumo della lamiera.
Per questo progetto, consegnato da pochi mesi, siamo partiti da un campione del coperchio finito che il cliente voleva ottenere.
Lo stampo passa attraverso una prima stazione di tranciatura, dove dalla striscia di banda stagnata si ottiene quella che in gergo è chiamata “pizza”, cioè un taglio sagomato semplice, senza nervature e imbutiture.
La seconda stazione riceve il componente dalla prima e forma il coperchio, imbutendolo e realizzando le tacche anti-incastro tipiche dei prodotti general line.
La terza stazione riceve il coperchio imbutito e ne arriccia i petali esterni verso l’esterno. Otteniamo così il prodotto finito.
Le dimensioni e il peso dello stampo (che può arrivare fino a 1.400 kg con i distanziali per la pressa in questione) hanno reso necessari vari test per mettere a punto il sistema dei tre passaggi. Per non spostare l’attrezzatura completa più volte dalla sede produttiva del cliente alla nostra a Parma, abbiamo realizzato delle piastre di adattamento per montare una stazione alla volta sulla nostra pressa di prova in officina.
Queste piastre sono state realizzate per gestire tutte e tre le operazioni: non rientrano nel sistema finale, ma velocizzano soltanto le prove.
Alla fine della prima fase di costruzione dello stampo abbiamo effettuato delle prove interne per collaudare la stazione di taglio.
La campionatura ottenuta dalle prove della prima stazione è stata utilizzata per i test della seconda stazione di imbutitura.
Per evitare la consueta formazione di grinze sulla superficie esterna del coperchio abbiamo prestato particolare attenzione al diametro della matrice di imbutitura, per ridurre il gioco a disposizione della lamiera per la formatura di tali grinze.
Abbiamo evitato la presenza di graffi nella parte interna del coperchio con un adeguato raggio del punzone.
Abbiamo utilizzato i campioni ottenuti per i test della terza stazione di ricciolatura, dove un’accurata lucidatura del ricciolatore permette di non rovinare la vernice e di ottimizzare la gestione di litografie speciali, con vernice opaca, molto sensibili ai graffi.
immagine
Il supporto e l’esperienza del cliente sono stati cruciali nell’effettuare le prove. Il lavoro di squadra ha portato a un ottimo risultato e per i nostri tecnici è stata un’altra preziosa opportunità di crescita e di confronto.
Perché è proprio questo che facciamo, ogni giorno: non smettere mai di imparare e migliorare. Insieme, sempre.